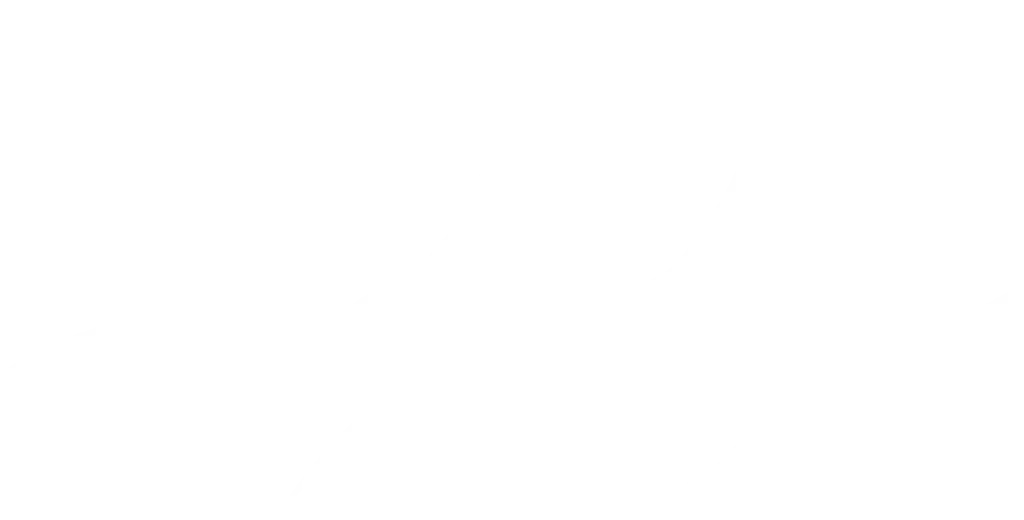
Air fills & testing
Safe, correct & compliant filling of compressed air cylinders is a highly specialised job. We have a fully HSE Compliant 300 bar filling station in house so call in have a coffee and get a fill while you wait. We welcome scuba divers, air gun enthusiasts and anyone who needs first class quality air fills.
The compressor
Any breathing air compliant compressor & filling station MUST undergo inspections, regular maintenance & have the following: a written scheme, quarterly air tests, a filling process, scuba cylinder testing (and stamps), air gun cylinder testing (and stamps).
Air gun cylinder users: filling of your cylinders MUST be done at a facility like ours. If your cylinder is filled from a source that isn’t compliant & doesn’t correctly control moisture levels during filling means you will be potentially exposed to a huge safety issue. The HSE guidance is very clear, and very eye-opening. Read it here.
The written scheme
This is a very comprehensive document that covers any pressure system that produces air over 0.5 bar pressure. It includes:
- identification of the items of plant or equipment within the system;
- those parts of the system which are to be examined;
- the nature of the examination required, including the inspection and testing to be carried out on any protective devices;
- the preparatory work needed for the item to be examined safely;
- where appropriate, the nature of any examination needed before the system is first used;
- the maximum interval between examinations;
- the critical parts of the system which, if modified or repaired, should be examined by a competent person before the system is used again;
- the name of the competent person certifying the written scheme of examination; and
- the date of certification.
Read more on the HSE Safety of pressure systems.
We have the schematic from the scheme displayed outside the filling station.
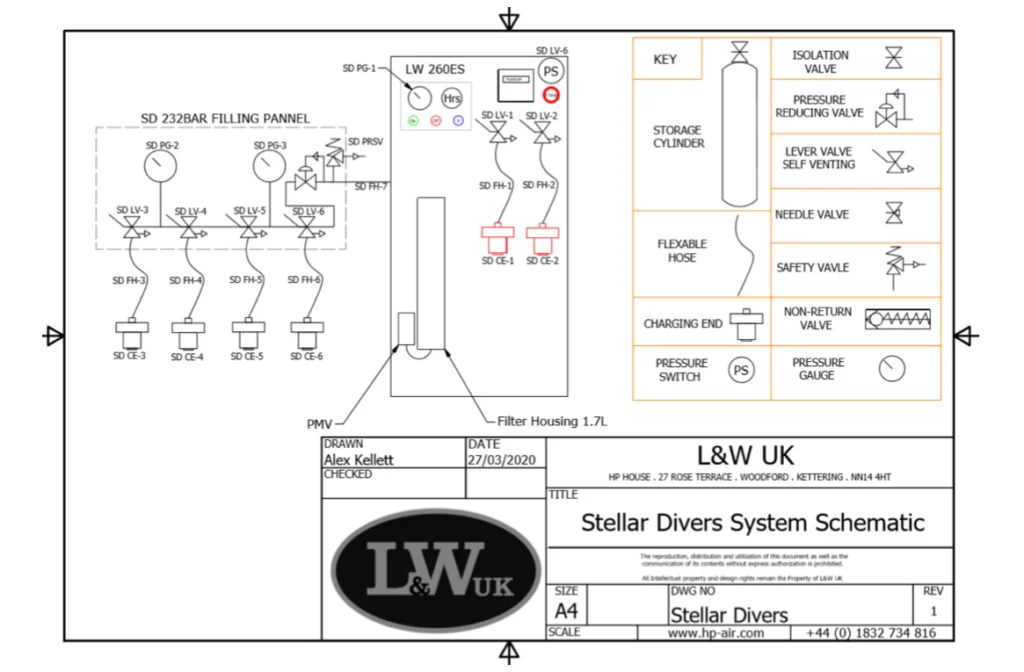
Quarterly air tests
At least each quarter a sample cylinder is filled from the compressor and then sent to an independent testing authority where the sample of air is checked. We display ours outside the filling station and you are welcome to ask questions. It is vital for cylinder & personal safety that the system be within the standards (The current cert is hanging in the Hub!).
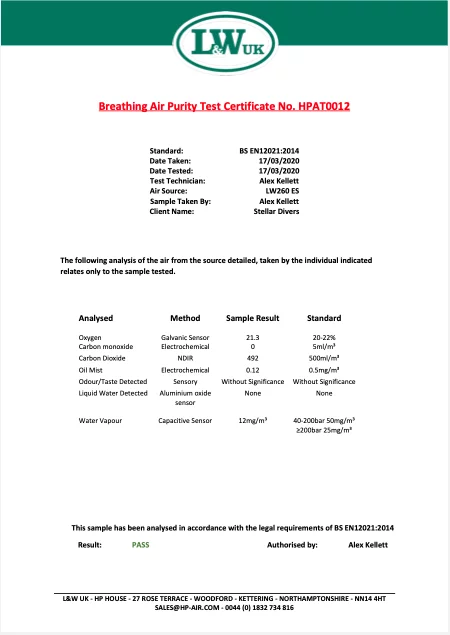
The filling process
When you bring you valuable cylinder to us for filling we will firstly check the test date on the cylinder.
If your cylinder is out of test we will show you this and then give you the choice to leave it with us for the relevant test.
If it is in test we will do an external visual inspection, checking for corrosion and general condition, if all is well we will fill to either 232 bar or 300 bar, depending on your cylinder type.
Scuba cylinder testing & stamps
When a cylinder has a “visual only” test it will be given a sticker on its shoulder indicating the date a hydrostatic test is required.
If a hydrostatic test has taken place there will be a stamp on the cylinders shoulder that will show the test centre number and date of test.
All breathing air scuba cylinders must be visually inspected every 2.5 years and hydrostatically tested every 5 years in line with BS EN 1968:2002 for steel gas containers, and BS EN 1802:2002 for aluminium gas containers.
If a visual test date is missed then the cylinder will undergo a hydrostatic test.
Air gun cylinder testing & stamps
An air gun (surface use only) cylinder is unique as it only requires a hydrostatic test every 5 years.
Once the hydrostatic test has taken place there will be a stamp on the cylinders shoulder that will show the test centre number and date of test in line with BS EN 1968:2002 for steel gas containers.
Visual testing
Each component of the cylinder has to be checked. The first task is to unscrew the valve and gauge (if fitted) from the neck, using a special tool while the bottle is held in a cradle with a strap wrench. Once those are out, a special gauge is used to check the threads it is a comprehensive check – the threads are examined for wear, damage and compatibility.
Next, the internal and external visual inspection is carried out. An endoscope is used to inspect the interior surfaces of the cylinder, to look for any signs of corrosion or damage. Some corrosion may be removed by shot-blasting – and in the case of external corrosion, the cylinder may also need to be re enamelled. Where corrosion has been corrected, an ultrasound scanner is then used to ensure the thickness of the metal in the cylinder’s wall is still acceptable.
Hydrostatic testing
In the case of a five-year ‘hydrostatic’ test, the cylinder is filled with water and immersed into a safety pressure tank, where it’s then submitted to about 1.5x its working pressure – around 450BAR for a 300BAR cylinder.
The purpose of this test is to measure the expansion of the cylinder; once the pressure is released, the expansion tank measures the degree to which the cylinder has expanded by displacement. In order to pass the hydrostatic test, the bottle must not expand more than five per cent of its original size.
Providing the cylinder goes through the test procedures, it’s then stamped with the year and month of test as well as the unique mark of the testing centre. A label clearly indicating that the bottle is for compressed breathing quality air is then added. A sticker is also applied to give an obvious reminder of the next retest date.
Should the cylinder fail its test the test centre won’t return it because, on safety grounds, it has to be scrapped, by cutting it up and then certified as having been destroyed.
Nitrox, tri-mix & oxygen
If you have a cylinder that is used for enriched air blends over 21% then it MUST be tested and O2 cleaned annually. You will receive an O2 clean sticker indicating the test date, this test does not replace the normal visual & hydrostatic tests.